Dielectric elastomers are electroactive polymers that can undergo significant reversible deformation under Maxwell stress, converting electrical energy into mechanical energy. They have advantages such as large deformation (>100%), high energy density, simple control, and ease of human-machine interaction, making them widely studied in the field of flexible actuators. As electro-mechanical energy conversion modules, the power density of these elastomers directly determines the output performance of flexible actuators. However, achieving high power density (>100 W/kg) typically relies on high driving electric fields (>40 MV/m), which places high demands on the insulation and operational safety of devices, limiting the application of dielectric elastomer-based flexible actuators. The power density of dielectric elastomers is approximately related to the fourth power of the driving electric field. Achieving high power density under low electric fields is a challenging problem.
Currently, common dielectric elastomers are mainly divided into two categories: acrylate and silicone rubber. Acrylate elastomers have high energy density but low response frequency, while silicone rubber elastomers exhibit the opposite properties. Recently, Professor Dan Zhimin’s team from the Department of Electrical Engineering and Applied Electronics (EEA) at Tsinghua University used two crosslinking agents with a large difference in molecular weight to construct a bimodal network of acrylate elastomers. The high molecular weight crosslinking agent provides the elastomer with high elasticity and low modulus, while the small molecular weight crosslinking agent shortens the average molecular weight between crosslinking points, accelerating stress transmission speed and improving the driving response frequency characteristics of the elastomer (Figure 1). This bimodal network of acrylate elastomers combines both high energy density and a driving frequency comparable to that of silicone rubber (~200 Hz). Under low driving electric fields, this bimodal network elastomer demonstrated high power density (154 W/kg @ 20 MV/m, 200 Hz), surpassing the typical value for mammalian skeletal muscle (50 W/kg). Furthermore, the researchers developed a flexible, non-magnetic rotating motor based on this advanced material and tested its rotational speed characteristics under various driving electric fields and frequencies. At a driving electric field of 19.6 MV/m and 125 Hz, the motor achieved a speed of 1245 rpm, much higher than previously reported acrylate elastomer motors (<200 rpm @ >40 MV/m) (Figure 2). This work, titled "A high-response-frequency bimodal network polyacrylate elastomer with ultrahigh power density under low electric field," was published in Nature Communications (Nature Communications (2024) 15:9819, https://doi.org/10.1038/s41467-024-54278-y). The first author of the paper is Dr. Yin Lijuan, a postdoctoral researcher from EEA. Collaborators include the Department of Mechanical Engineering and the Department of Chemistry of Tsinghua University, the School of Electrical Engineering of Zhengzhou University, and the School of Electrical Engineering of Xi'an Jiaotong University. The research was supported by the National Natural Science Foundation of China (key fund, general fund, and youth fund) and the China Postdoctoral Science Foundation, among others.

Construction, Microstructure, and Composition Characterization of Bimodal Network Acrylate Elastomers
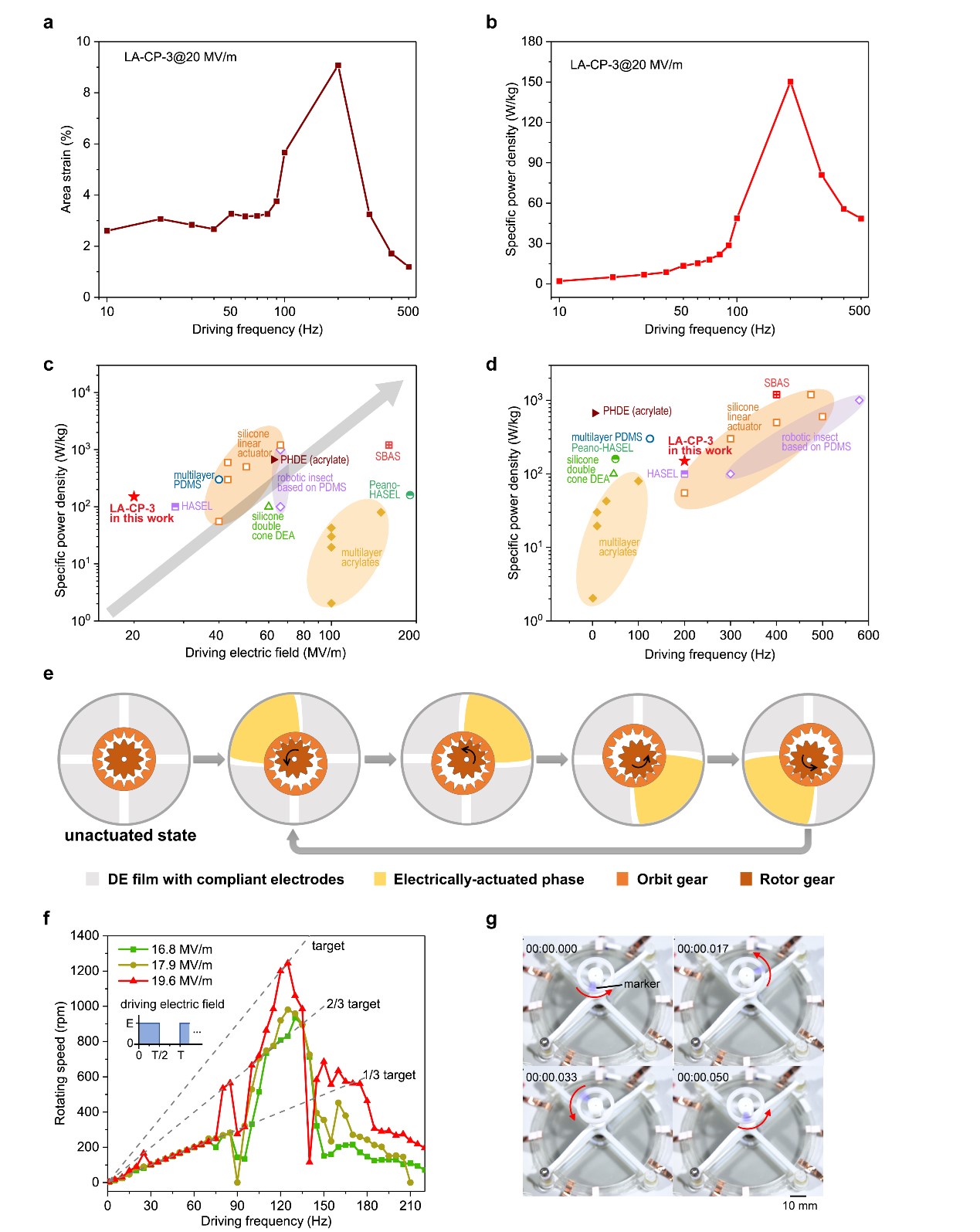
Power Density Characteristics of Acrylate Elastomers and Output Performance of Flexible Rotating Motors
Professor Dan Zhimin’s team has been conducting research in the fields of acrylate elastomers and flexible rotating motors for many years, focusing on the relationship between the structure and performance of dielectric elastomers and their impact on the output performance of flexible motors. In 2021, they published a paper titled “Soft, tough, and fast polyacrylate dielectric elastomer for non-magnetic motor” in Nature Communications, which explored the low-field drive and fast response issues of acrylate elastomers (Nature Communications (2021) 12:4517, https://doi.org/10.1038/s41467-021-24851-w). Based on years of research in the field of dielectric elastomers, the team has been granted major science and technology projects from central ministries and commissions, as well as key and youth projects from the National Natural Science Foundation of China.